Nestled in the foothills of North Fayston, just outside of Moretown in Vermont’s scenic Mad River Valley, lies a burgeoning community of tiny homes with a purpose. One Vermonter is hoping to change the face of housing access and affordability in a region where land and home values are rapidly increasing. Meet Abby Dreyer, the artist, gallery owner, and pottery teacher whose vision is to create a community of affordable housing on her 120-acre property through building six tiny homes and the infrastructure to support a vibrant, close-knit community of people living in them. According to Abby, the project has had its challenges, namely around acquiring the proper zoning and permits to create such a community.
But after advocating for her vision and raising awareness around the housing crisis in the Mad River Valley, she was granted the necessary permits to begin laying the groundwork for her beautiful vision.
Eventually, there will be six small dwellings on her property, with up to three of the six lots zoned for tiny homes on wheels. She also maintains a wood and metal shop with a 2nd story apartment, in addition to her own home.
The newest addition to the property, recently completed by TimberHomes Vermont, will be a gathering space for the future residents of her woodland enclave, as well as additional storage for those people. The timber frame barn will also house Abby’s tractor and other farm implements, and a seasonal cache of firewood. Drawing on classic monitor-style barns for inspiration, this 28’x36′ structure has a 12’x36′ second story full of windows that will become the gathering space for group events on the land. The eastern white pine frame is visible in its entirety, and includes a great deal of heritage joinery amidst its post and beam construction. Scarf joints, half laps, and down braces decorate this sturdy building, and the upper story includes a pair of diversed X Braces that were integrated into the frame using stereotomy, a developed drawing technique that allows for complex timbers to be joined together using little (if any) numerical math. Read more about stereotomy at our blog post here.
One of the two signature X braces that adorn the upper level of this structure
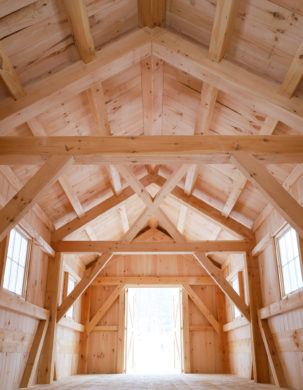
The stereotomical elements in all their glory
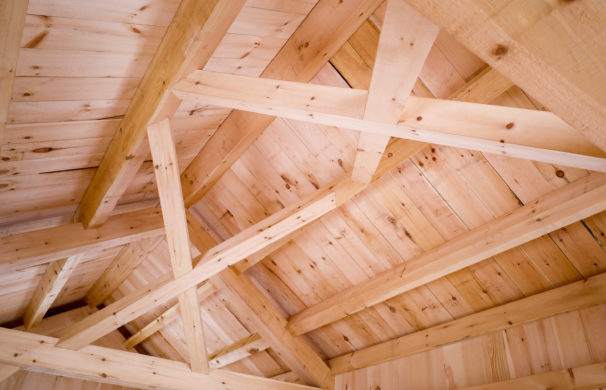
In addition to the mixed-use purpose of this barn, and the variety of handcrafted timberframe joinery, this project was also unique among TimberHomes Vermont’s projects in that it was our first all-company hand raising. In lieu of a crane or other machinery, all 17 TimberGnomes gathered together and lifted each timber into place by hand, following a raising script developed by the project site lead and executed by one of the company’s founding partners. It was a team-building exercise just as much as a barn-building exercise, and at the end of the day the crew was feeling accomplished and proud of what we can achieve with human power and great communication.
Getting down to the technical details, this barn is built from locally-milled eastern white pine timbers, and clad in locally milled shiplap siding. The lower roof sections feature a common rafter system, while the upper roof uses principle rafters supporting purlins. All doors were built in-house by TimberHomes, as were casements for the nine windows that bring light into this structure. The lower level of this barn was raised in “walls”, cross sections along the 36′ length that are each unique, while the upper monitor section was raised in four more-or-less identical 12′ wide bents. Three storage units will be divided among up to six future tenants at Abby’s tiny house community, and their soaring height and sizeable footprint will allow those who use them to make the most of the space. Sliding barn doors allow for full access to the innermost section of the lower level, allowing the client to park her tractor inside and out of the elements. For the upper level, there are plans to build a large harvest table and countertop (from slabs milled out of trees that were growing on the land) for hosting community gatherings in the spring, summer, and fall. A large covered area on the west side of the structure will be ideal for stacking and drying firewood, as well as storing seasonal equipment.
After the all-company hand raising, a crew of four stayed on site for the remaining six weeks to finish this gorgeous multi-use barn. Site work wrapped up just as the first big snow fell, blanketing this barn in a coat of pure white Vermont snow.